Overview of Beryllium Copper Material
1. Introduction to the General Properties and Uses of Beryllium Copper
Beryllium copper is an alloy of copper with small amounts of beryllium, known for its high strength, hardness, and electrical conductivity. Widely used in applications requiring precise mechanical components, connectors, and springs, beryllium copper offers excellent performance in challenging environments.
2. Different Types of Beryllium Copper Alloys and Their Properties
- C17200 (Beryllium Copper): Common alloy with good conductivity and machinability.
- Example: Springs, electrical contacts.
- Properties: High strength, excellent thermal and electrical conductivity.
CNC Punching Beryllium Copper Basics
1. Basic Principle of CNC Punching
CNC punching involves using a punch and die to create holes and features in sheet metal. This process is highly efficient for mass production and allows for the creation of intricate shapes in beryllium copper.
2. Composition and Function of CNC Punching Equipment
CNC punching equipment includes a punch press with a turret or tool magazine. The control system manages tool selection, positioning, and punching operations, ensuring precision in fabricating beryllium copper components.
3. Basic Steps of Punching Process
- Sheet Loading: Securely fix the beryllium copper sheet on the punching machine.
- Tool Selection: Choose appropriate punches and dies for desired features.
- Punching Operation: Execute the CNC program to punch holes and shapes in the beryllium copper sheet.
CNC Punching Beryllium Copper Tools and Equipment
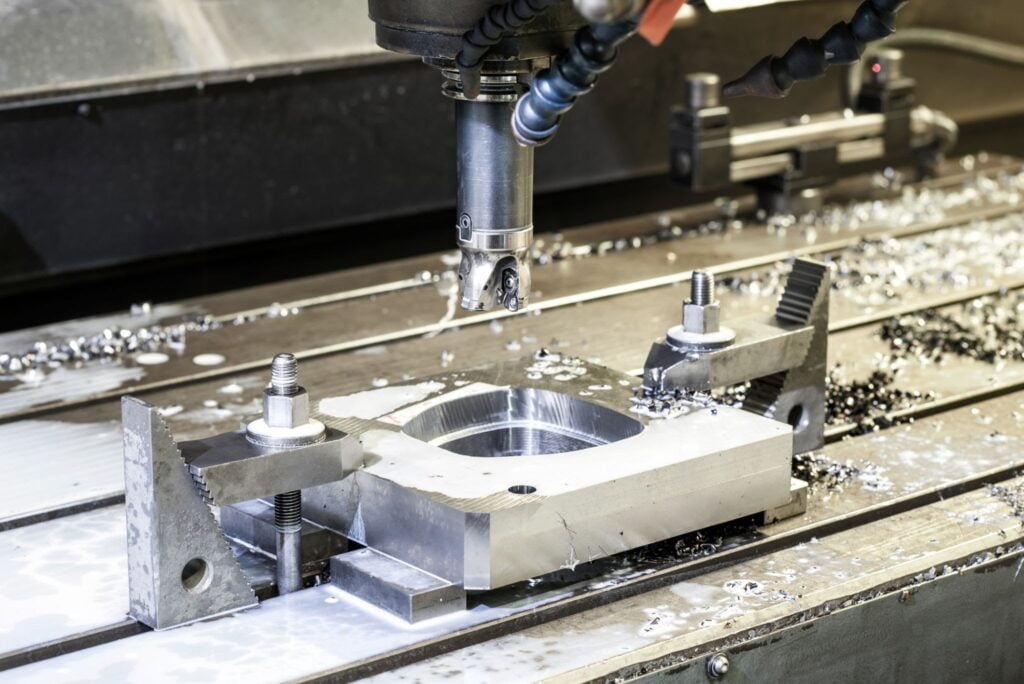
1. Types and Characteristics of CNC Punching Machines
- Turret Punch Press: Equipped with a rotating turret holding multiple tools.
- Example: CNC turret punch press with beryllium copper-compatible features.
- Characteristics: High-speed, versatile punching capabilities.
- Single-Station Punch Press: Suited for smaller production runs.
- Example: CNC punch press with single-station capabilities.
- Characteristics: Simplicity and flexibility in tool setup.
2. Different Types of Punching Tools
- Round Punches: Common for creating circular holes.
- Example: Round punch for creating fastener holes in beryllium copper.
- Characteristics: Versatile for various hole sizes.
- Rectangular Punches: Used for creating slots and straight edges.
- Example: Rectangular punch for slotting beryllium copper sheets.
- Characteristics: Ideal for creating elongated features.
- Embossing Tools: Add raised or recessed features.
- Example: CNC embossing tool for branding beryllium copper components.
- Characteristics: Enhances aesthetic and functional properties.
3. Selection and Use of Punching Lubricants
- Dry Lubricants: Minimize friction during punching.
- Example: Solid film lubricant for beryllium copper punching.
- Use: Reduces tool wear and improves surface finish.
- Wet Lubricants: Water-based lubricants for cooling.
- Example: Water-soluble lubricant for efficient beryllium copper punching.
- Use: Prevents overheating during the punching process.
CNC Punching Beryllium Copper Preparation before Machining
1. Sheet Fixing and Clamping Methods
- Vacuum Table: Securely holds thin beryllium copper sheets.
- Example: CNC punching machine with a vacuum table.
- Method: Applies suction to hold the sheet in place.
- Clamps and Pins: Suitable for thicker beryllium copper sheets.
- Example: CNC punching machine with adjustable clamps.
- Method: Secures the sheet using mechanical clamping.
2. CNC Program Writing and Debugging
- CAD/CAM Software: Design and program the punching operation.
- Example: Use software like AutoCAD or SolidWorks.
- Debugging: Simulate the program to verify toolpaths and hole locations.
- Toolpath Optimization: Ensure efficient tool movement.
- Example: Optimize toolpaths to minimize travel distance.
- Debugging: Verify and adjust toolpaths for accuracy.
3. Tool Selection and Setting
- Beryllium Copper-Compatible Punches and Dies: Choose materials suitable for beryllium copper.
- Example: Carbide punches and dies for beryllium copper punching.
- Setting: Optimal clearance and alignment for efficient punching.
- Tool Rotation Control: Ensure correct tool positioning.
- Example: CNC punch press with automatic tool rotation.
- Setting: Program rotation angles for each tool.
CNC Punching Beryllium Copper Punching Parameters and Techniques
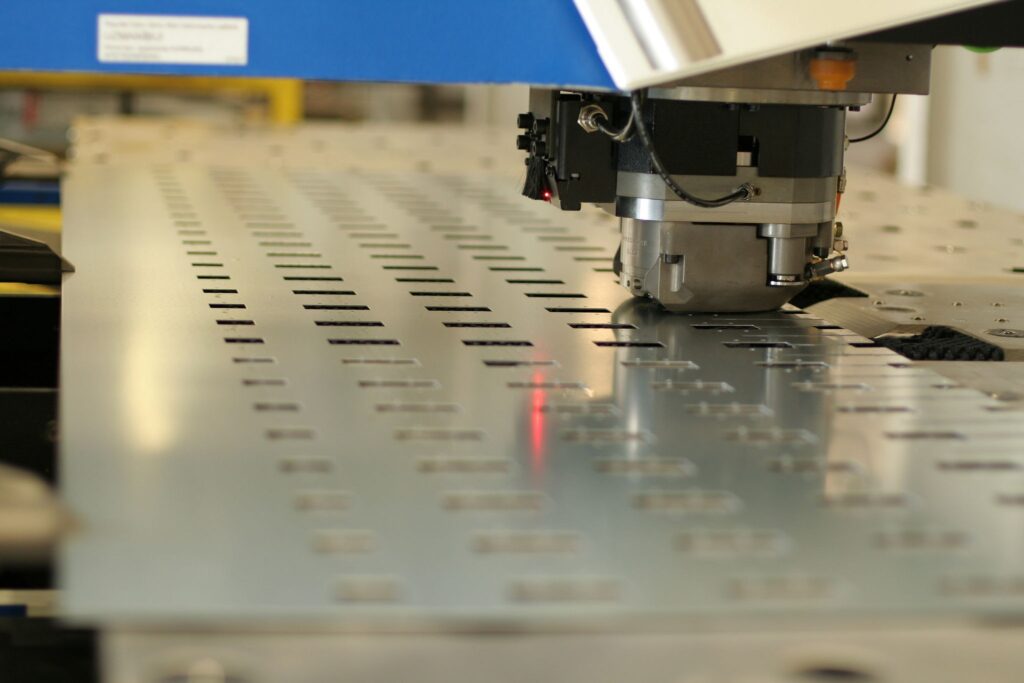
1. Selection of Punching Speed, Feed Rate, and Clearance
- Punching Speed: Adjust based on beryllium copper sheet thickness.
- Example: Higher speed for thin beryllium copper sheets.
- Solution: Optimize for material thickness to prevent distortion.
- Feed Rate: Determines punching efficiency.
- Example: Higher feed for faster production.
- Solution: Adjust for optimal efficiency without compromising accuracy.
- Clearance: Gap between punch and die.
- Example: Larger clearance for thicker beryllium copper.
- Solution: Optimize clearance to prevent burrs and tool wear.
2. Punching Characteristics of Different Beryllium Copper Alloys
- C17200 (Beryllium Copper): High strength and hardness.
- Example: Optimal feed rates for efficient punching.
- Solution: Tailor parameters for alloy-specific properties.
3. How to Avoid Punching Distortion and Burr Formation
- Fixture Design: Minimize unsupported areas during punching.
- Example: Use backing plates for support.
- Solution: Design fixtures to reduce distortion.
- Tool Sharpness: Regularly check and sharpen punching tools.
- Example: Implement a tool maintenance schedule.
- Solution: Ensure sharp tools for clean cuts and reduced burr formation.
CNC Punching Beryllium Copper Common Problems and Solutions
1. Common Problems in CNC Punching Beryllium Copper
- Burr Formation: Addressed through tool sharpness and clearance.
- Example: Increase tool clearance for smoother edges.
- Solution: Regularly inspect and sharpen tools.
- Distortion: Minimized through proper fixture design.
- Example: Optimize fixture support for the beryllium copper sheet.
- Solution: Ensure even support to prevent distortion.
- Misalignment of Holes: Checked through accurate toolpath programming.
- Example: Verify toolpaths in simulation software.
- Solution: Debug and optimize toolpaths for precision.
2. Steps and Methods to Solve These Problems
- Regular Tool Maintenance: Sharpen and inspect punches and dies.
- Example: Establish a routine for tool maintenance.
- Solution: Replace or sharpen tools as needed.
- Optimized Fixture Design: Ensure proper support during punching.
- Example: Use custom fixtures for different beryllium copper parts.
- Solution: Design fixtures to minimize distortion and misalignment.
Table for CNC Punching Beryllium Copper Parameters
Metal Type | Punching Tool | Punching Speed (mm/min) | Punching Force (kN) | Tool Material | Tool Life (cycles) |
---|---|---|---|---|---|
Beryllium Copper | Carbide Punch and Die | 320 | 55 | Carbide | 50,000 |
Beryllium Copper | Rectangular Punch | 340 | 60 | High-Speed Steel | 45,000 |
Beryllium Copper | Embossing Tool | 300 | 50 | Tool Steel | 48,000 |
CNC Machining Samples
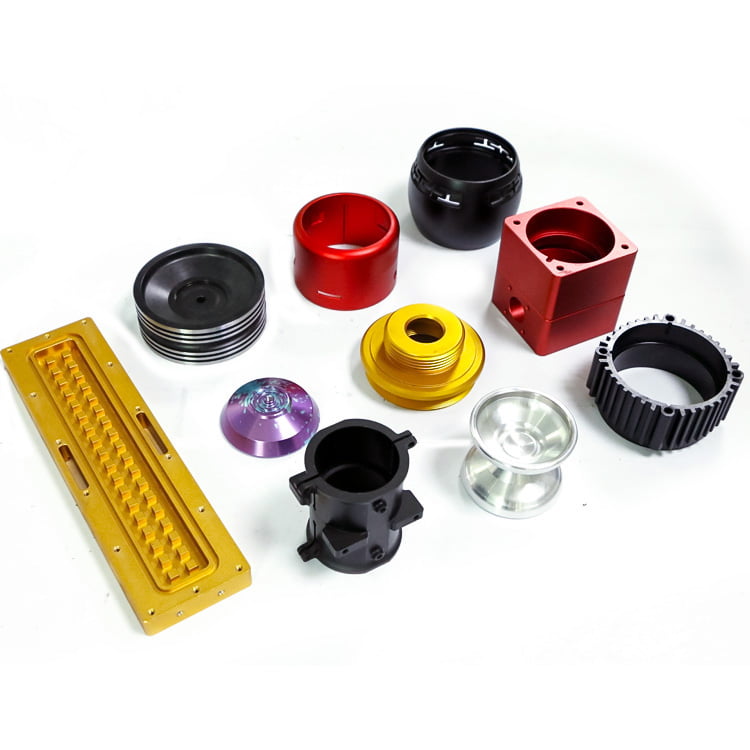
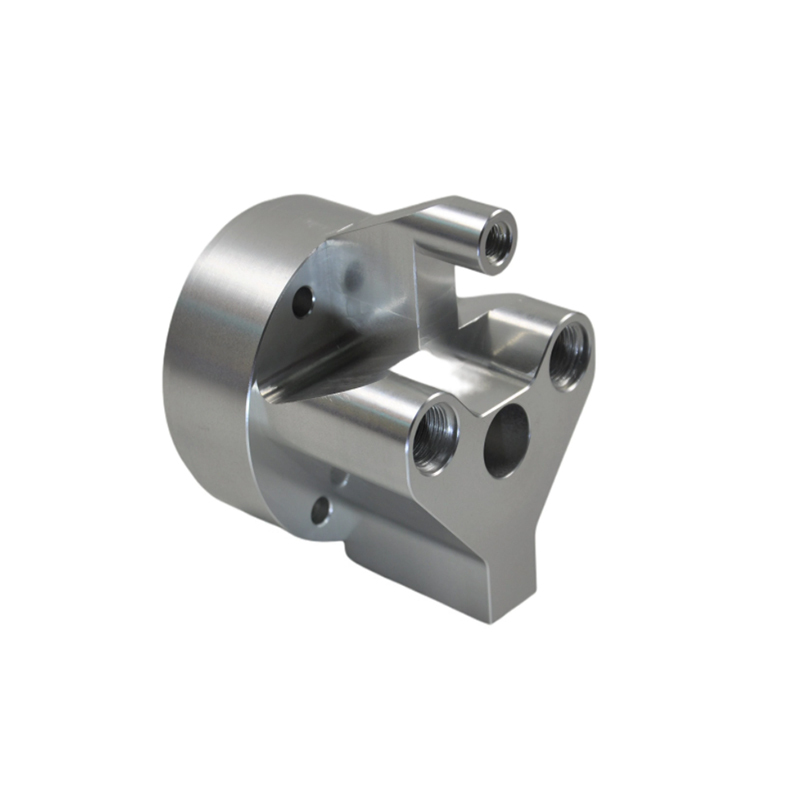
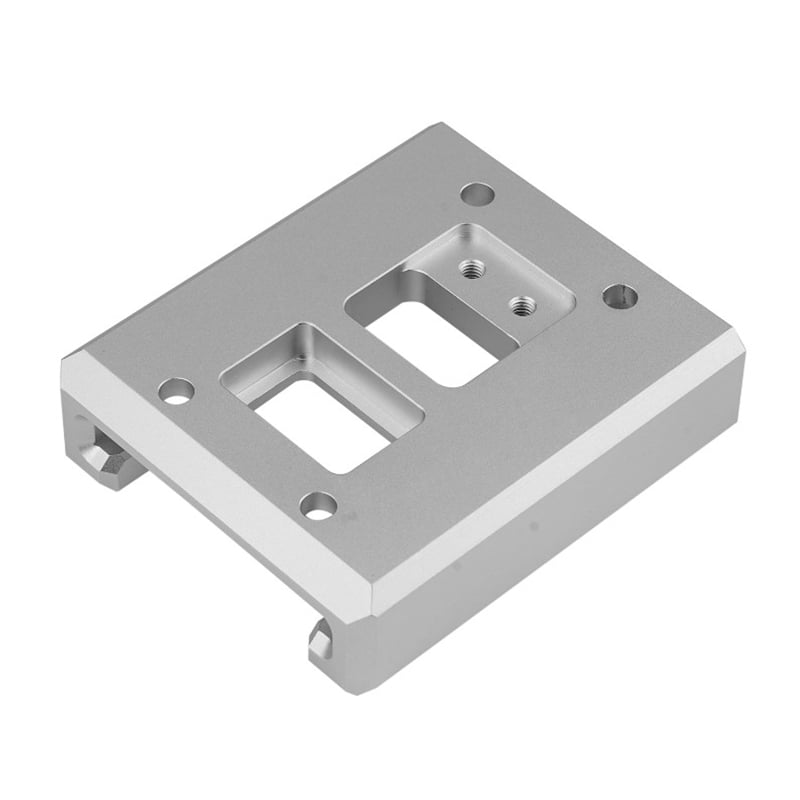
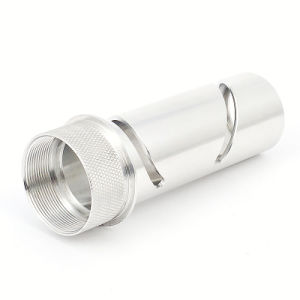
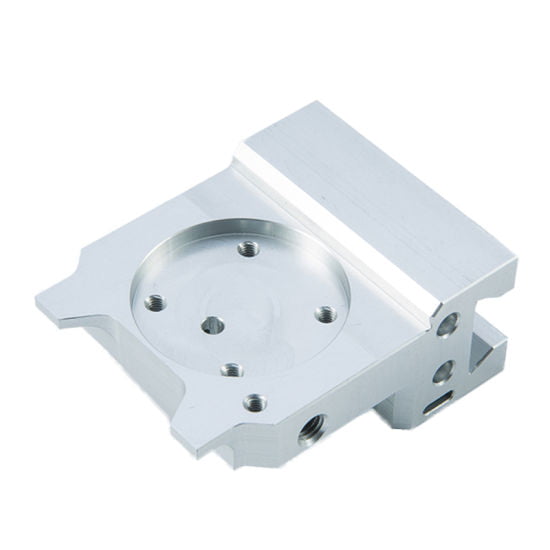
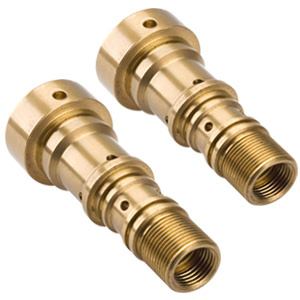
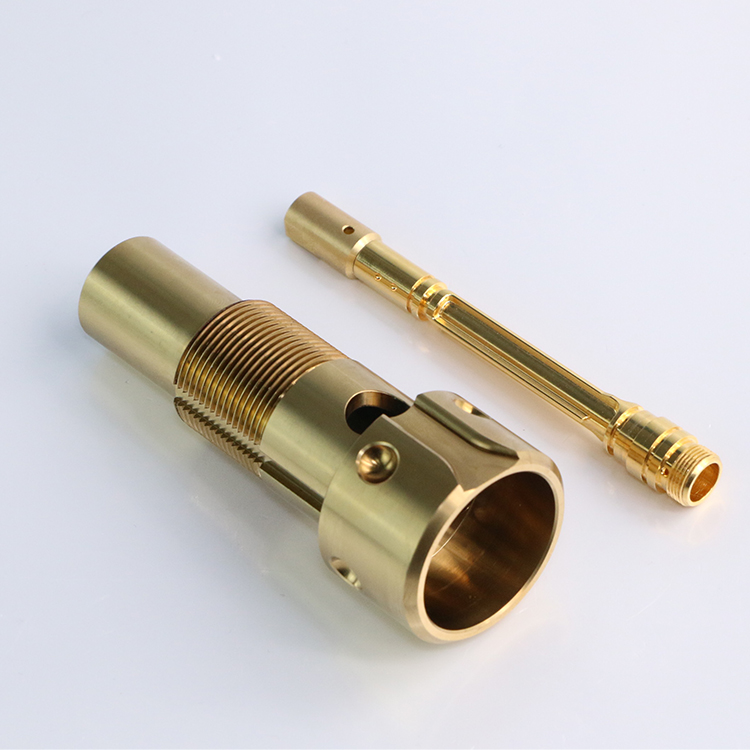
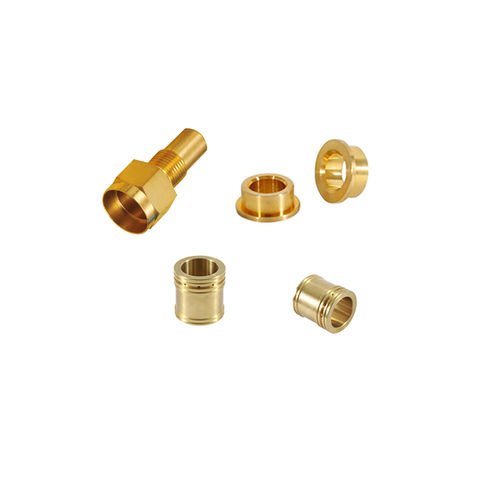
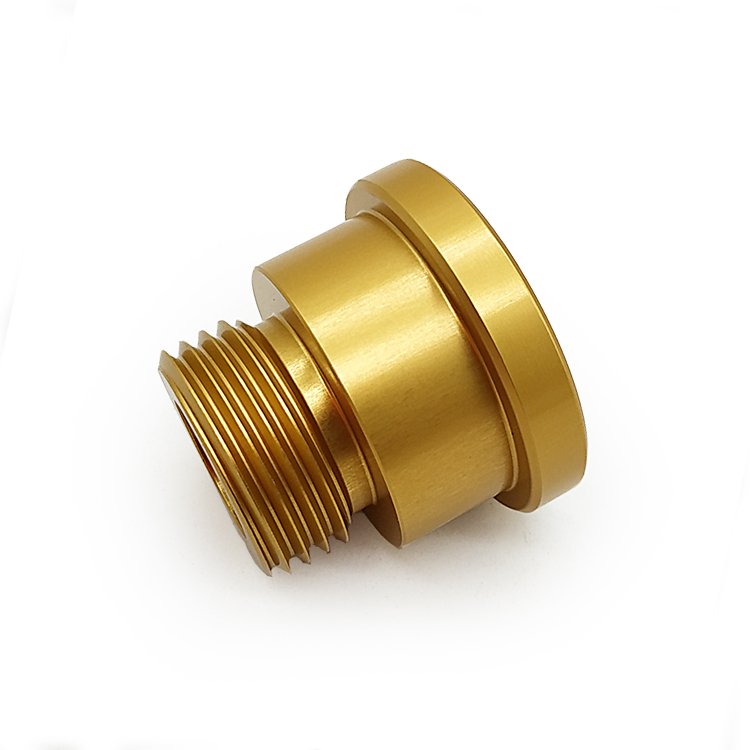
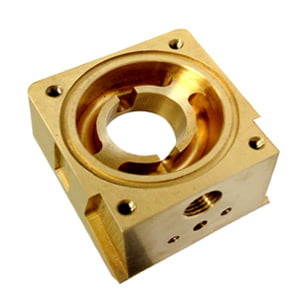
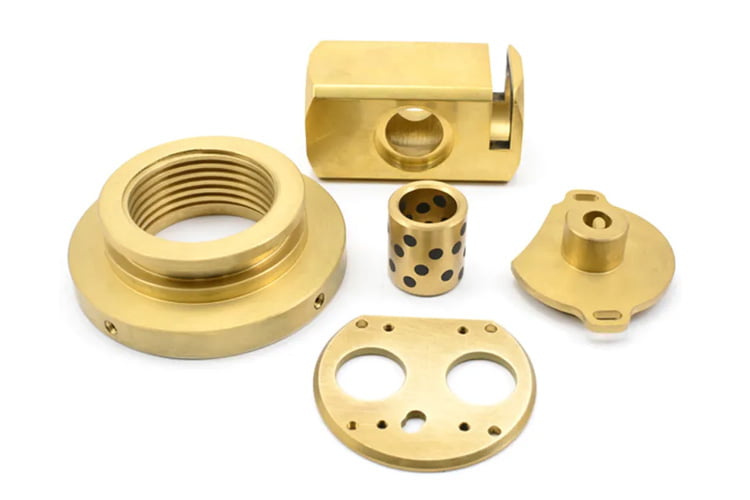
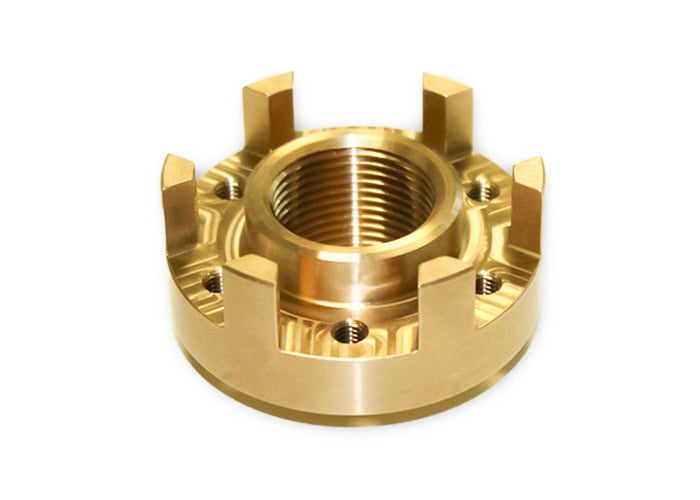
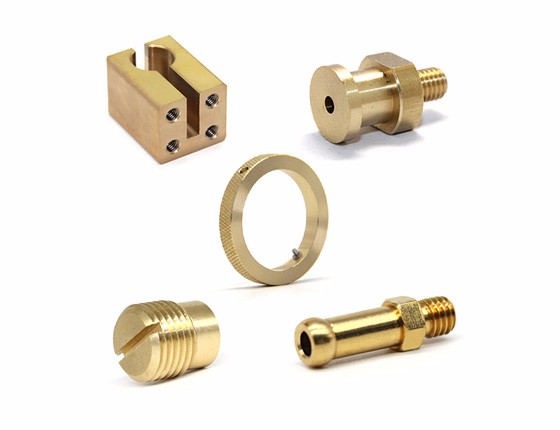
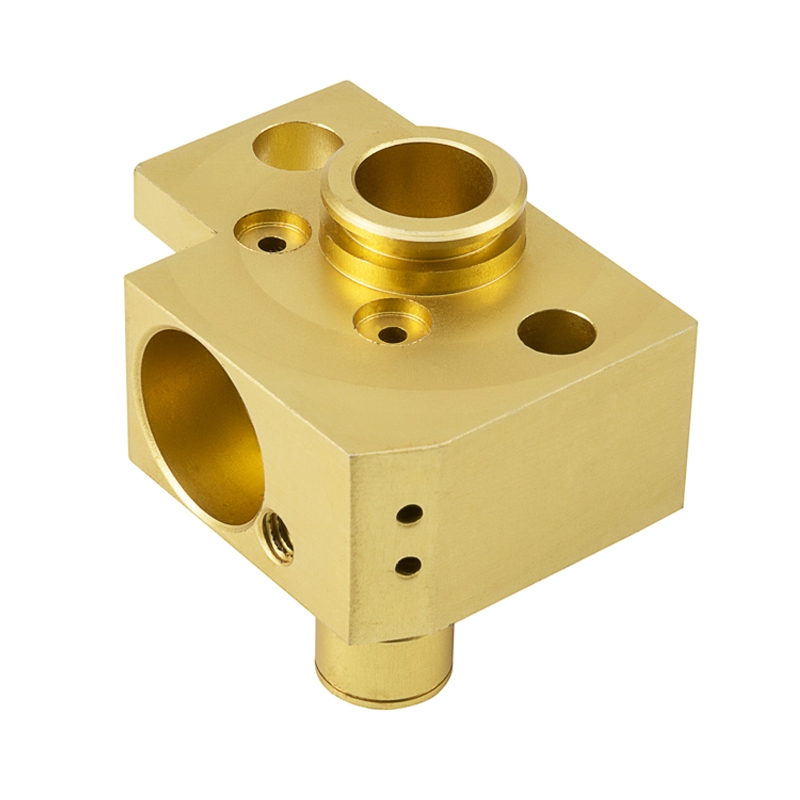
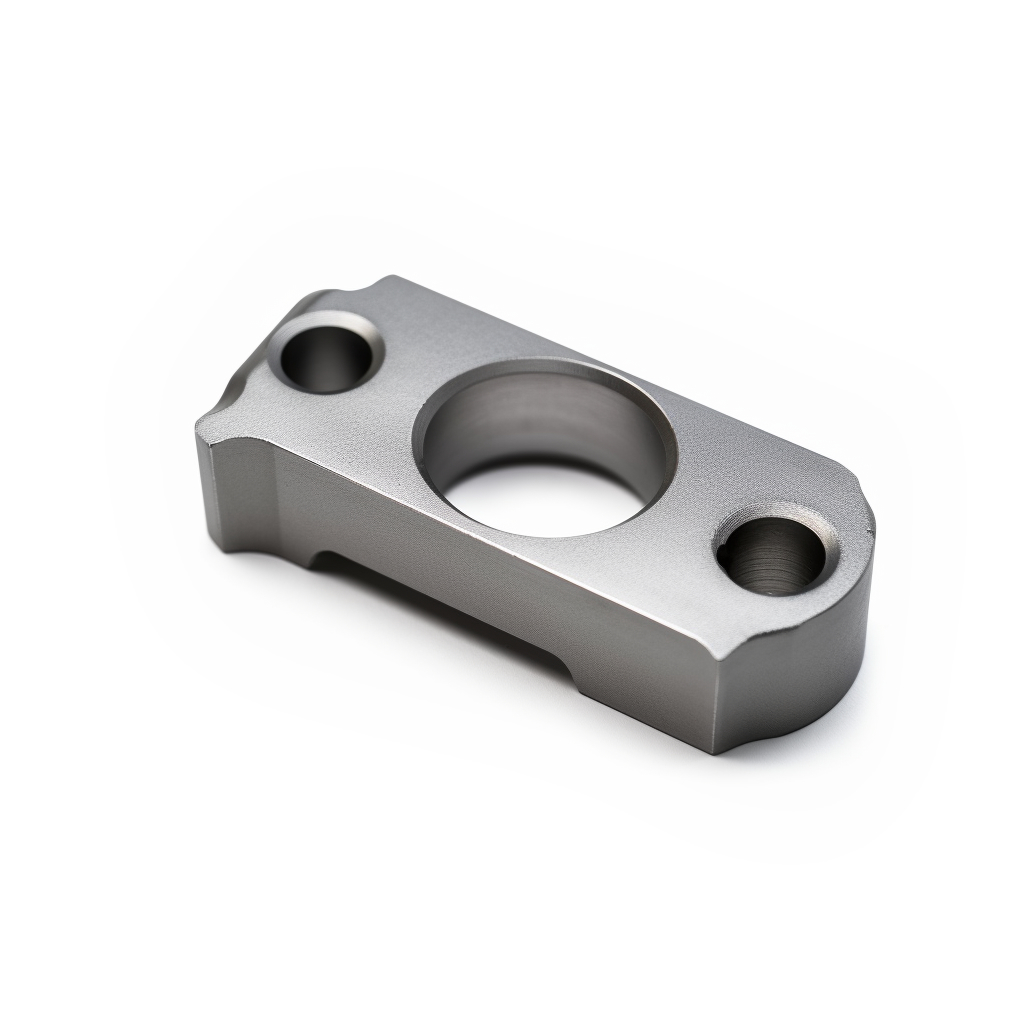
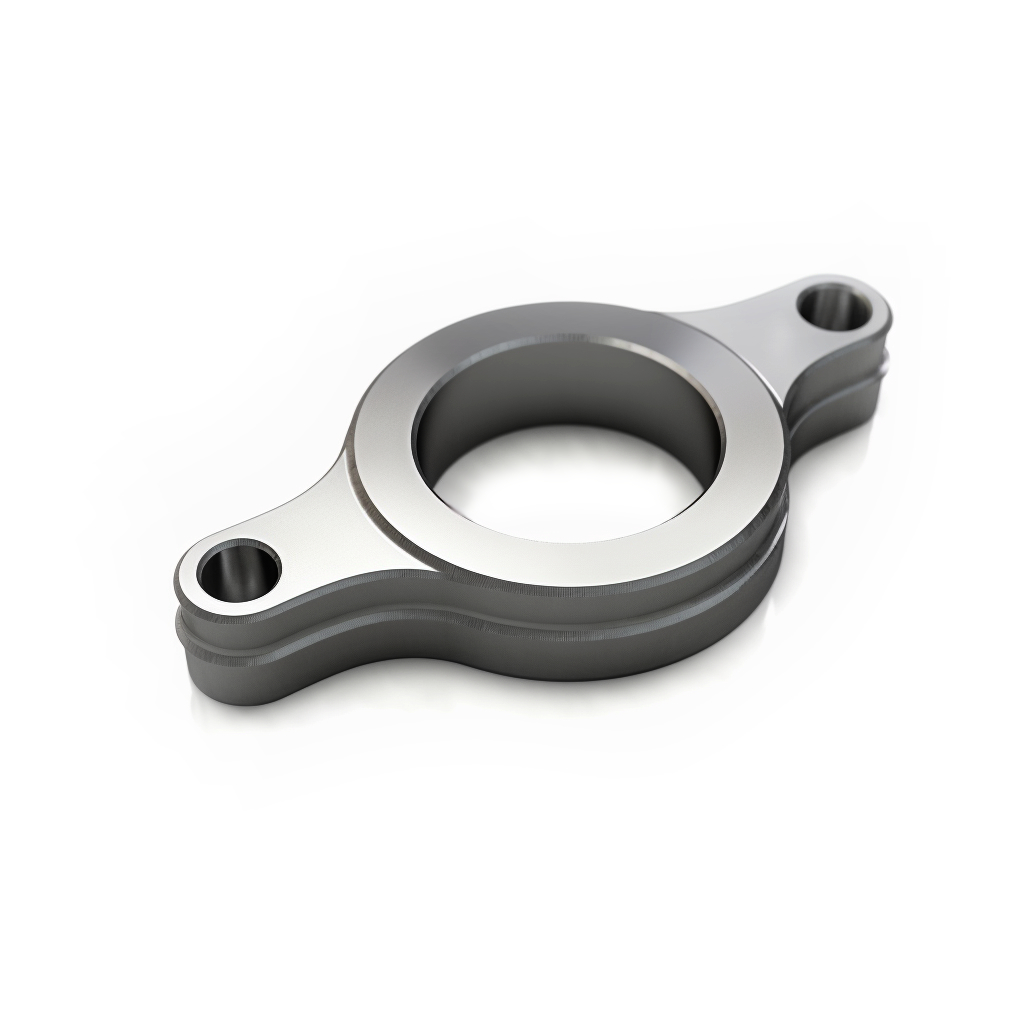
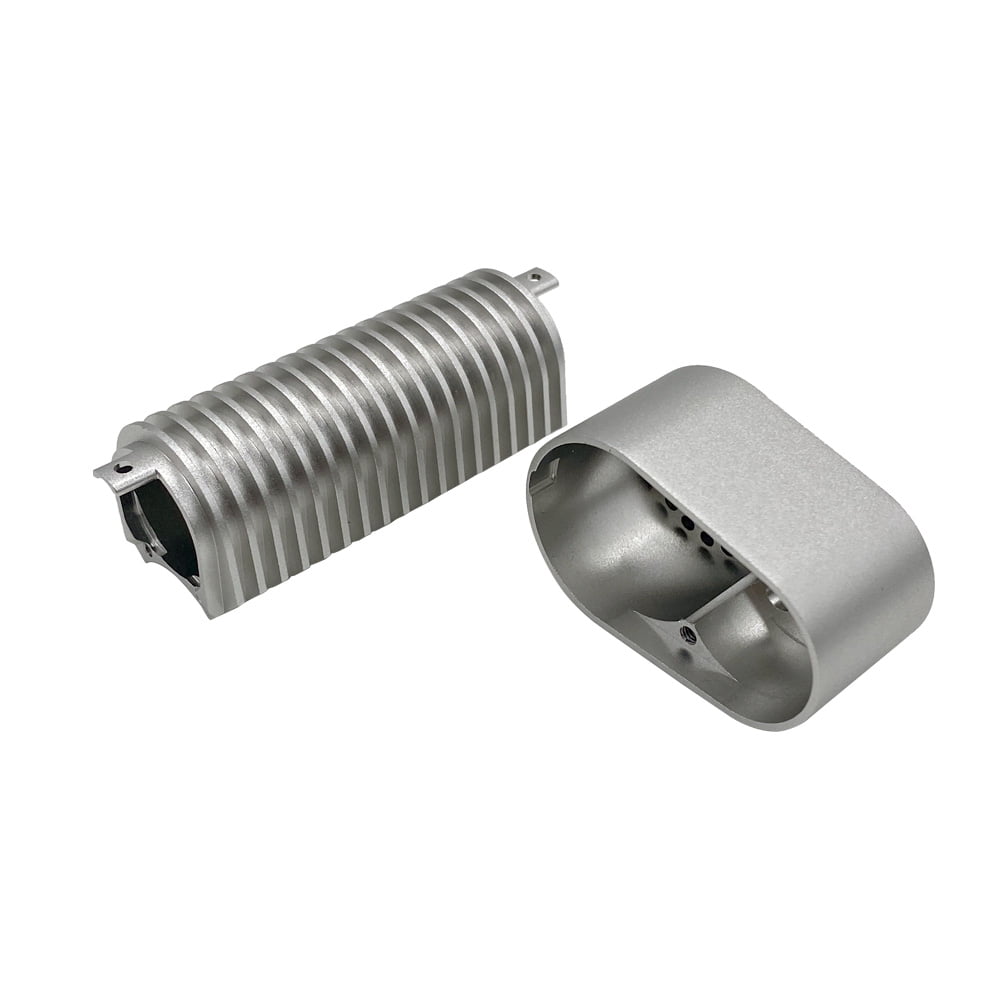
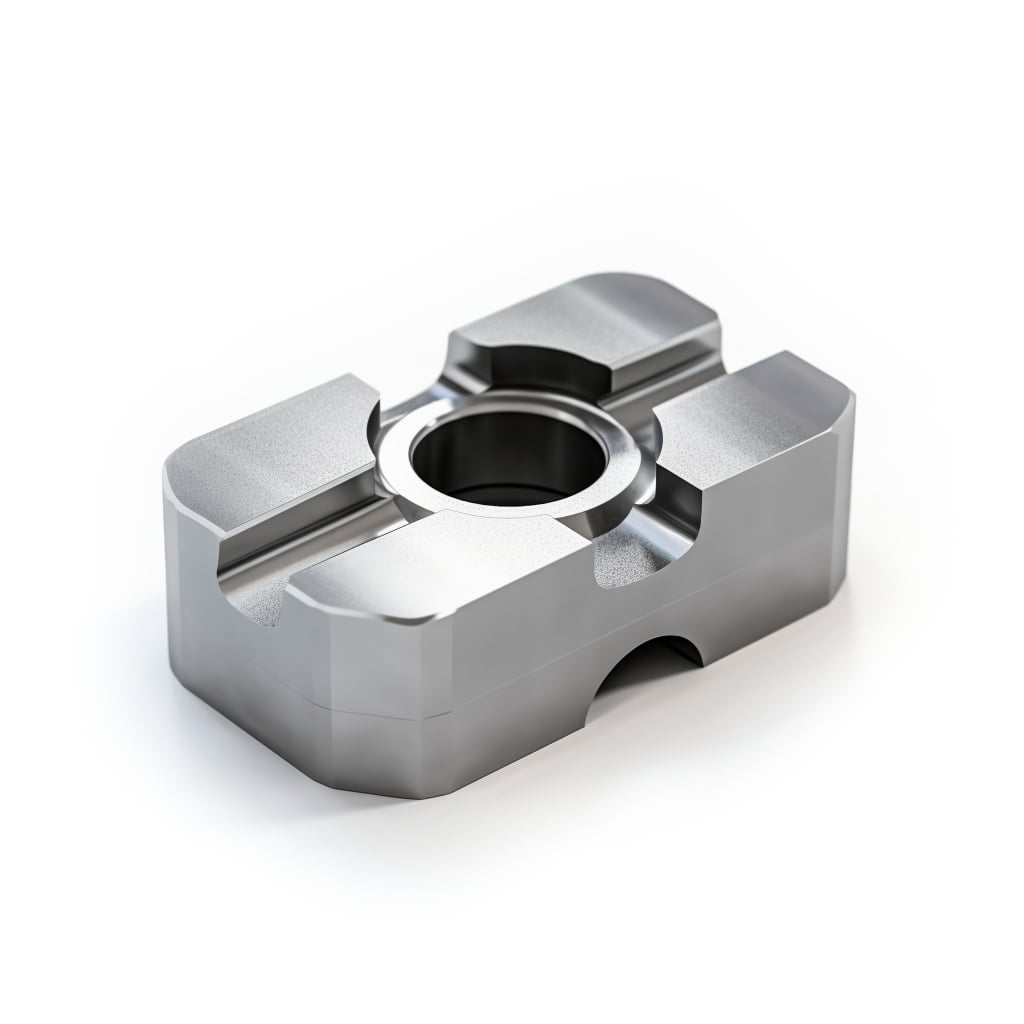
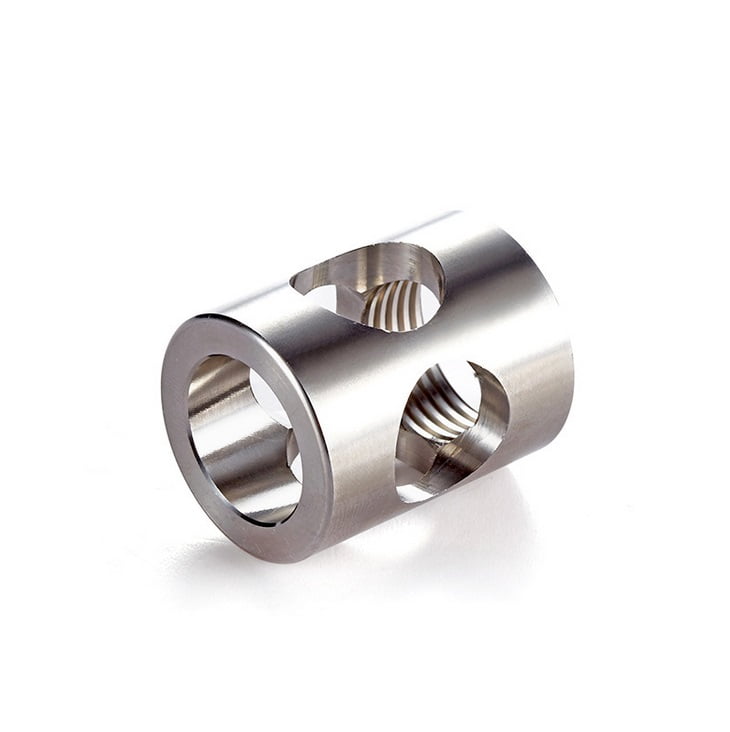
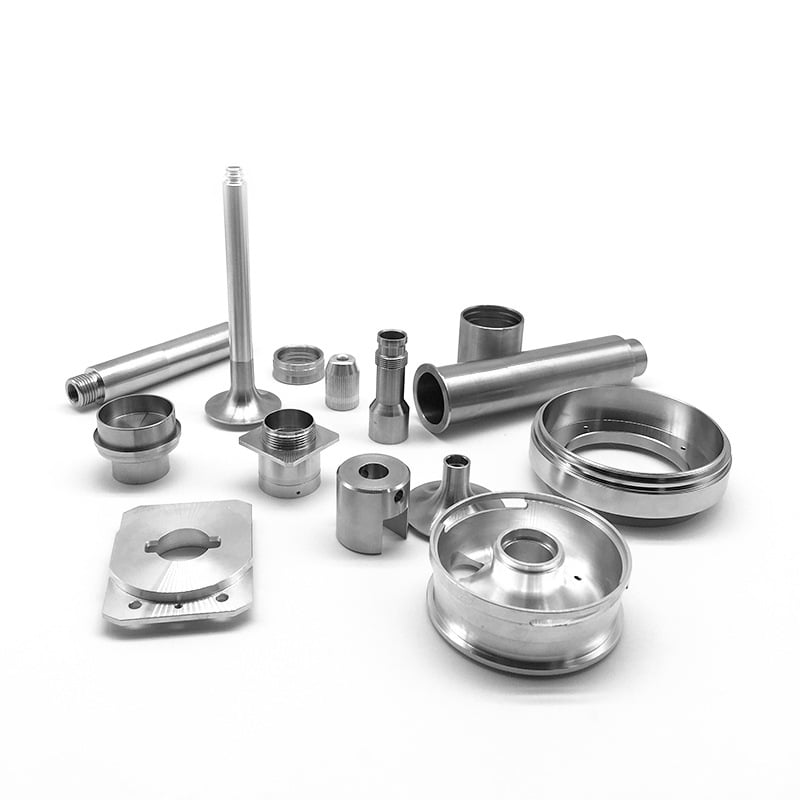
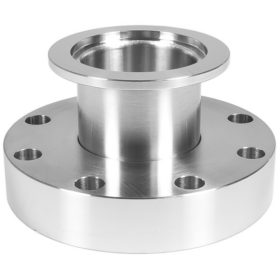
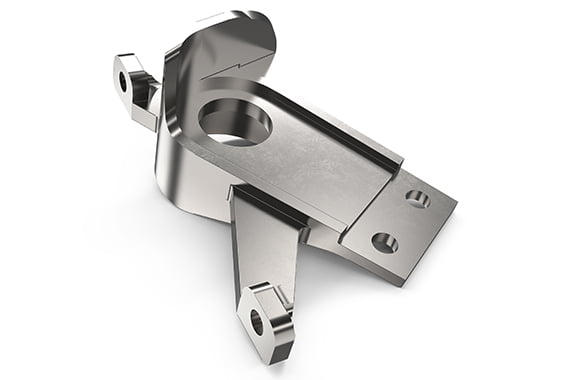
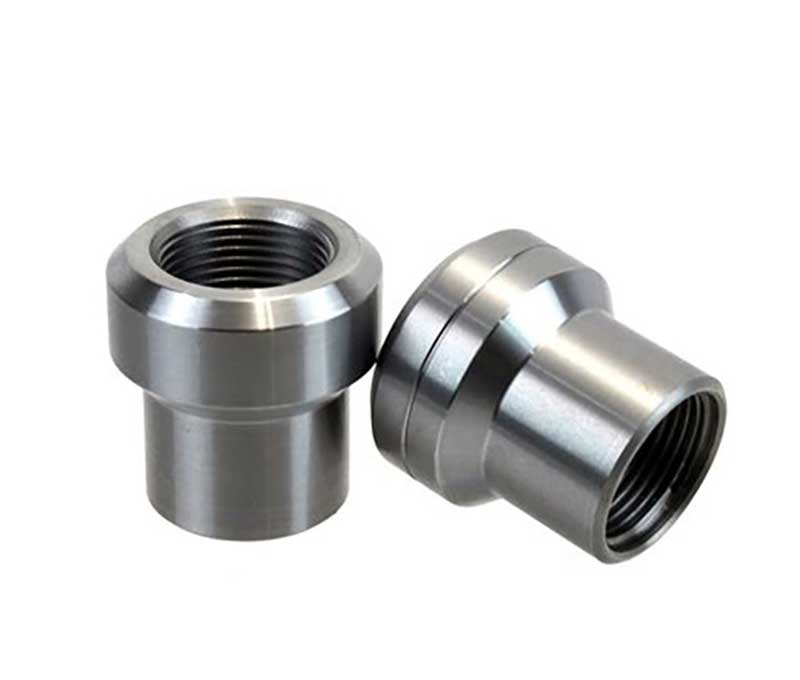
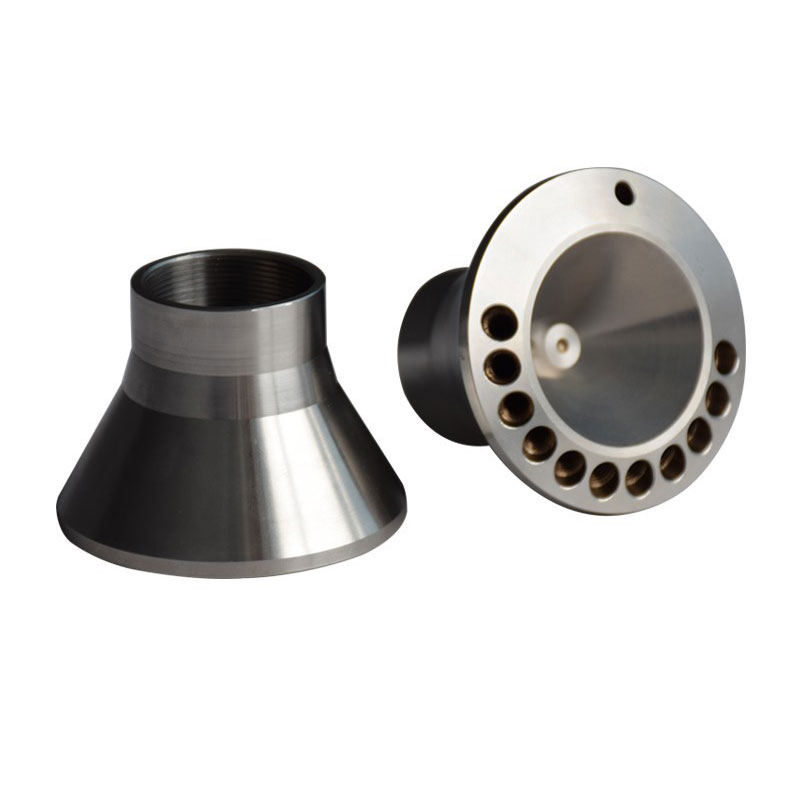
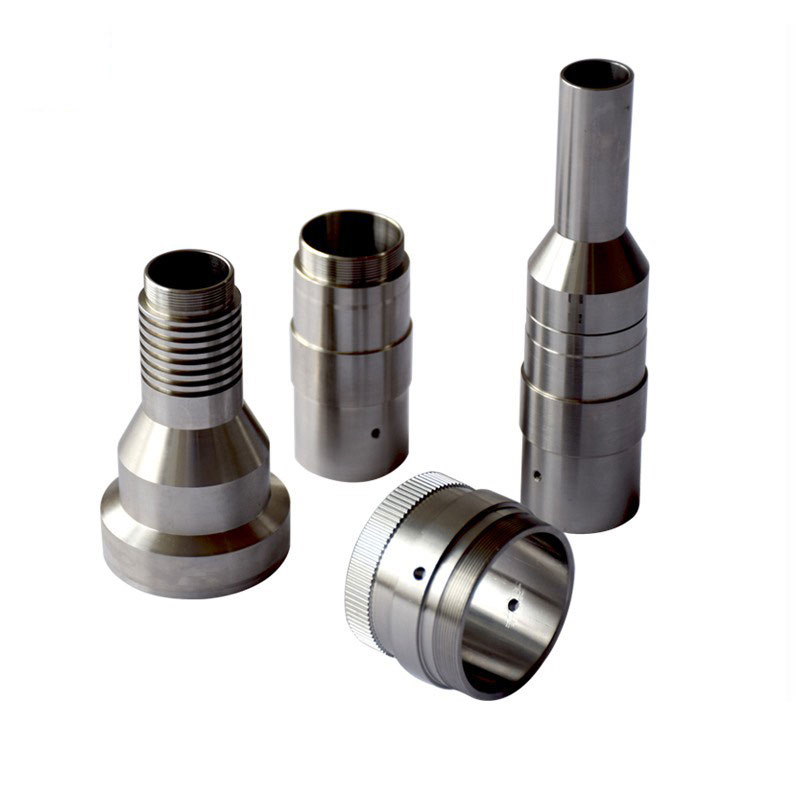
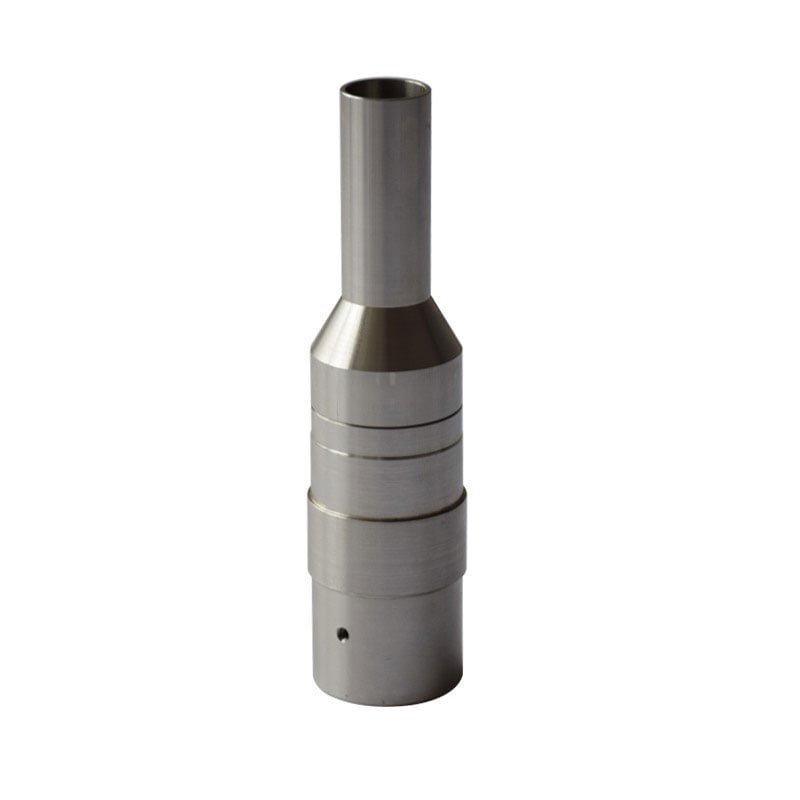
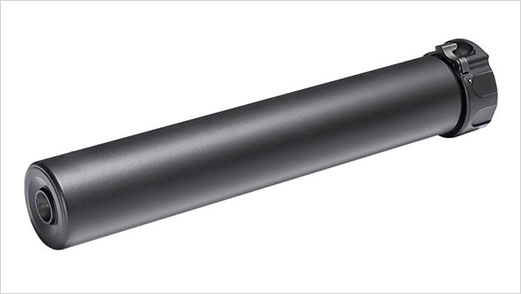
If you need custom metal fabrication, please don’t hesitate to contact us immediately. We will provide you with the appropriate processing price within 2 days of receiving your material.
View V&T service reviews
this company is my go to! have used them multiple times great prices V&T is the best to work with!
Robert James


this company is my go to! have used them multiple times great prices V&T is the best to work with!
Robert James
Quality yet cheap. Service Staff was very friendly and helpful. Measurements of parts was very accurate for the anodized aluminium, and prices were very competitive
Jerimiah D.


Quality yet cheap. Service Staff was very friendly and helpful. Measurements of parts was very accurate for the anodized aluminium, and prices were very competitive
Jerimiah D.
Good quality of the product, the color matches the photos. The milling machine operator is good. Thanks.
Francy J.


Good quality of the product, the color matches the photos. The milling machine operator is good. Thanks.
Francy J.
If you can deal with V&T you will have a very good experience. Sometimes they can be quite late though, and communication was bad for a while. I have dealt with this company for 3 years now. Mostly satisfied
Marianna B.


If you can deal with V&T you will have a very good experience. Sometimes they can be quite late though, and communication was bad for a while. I have dealt with this company for 3 years now. Mostly satisfied